Automated Drone Monitoring System
Objective: Subsurface Insights sells recommendations to farmers on how to increase agricultural yield and decrease crop loss as part of a Software as a Service (SaaS) model. They currently use data from ground-based sensors and satellites but would like to further augment the data collection by using sensor data collected from 400 feet above the ground so as to improve their recommendations. There is currently no system that can sample this data regularly and autonomously within their budget. A system which can accomplish this goal is very complex so Subsurface Insights has sponsored our team comprised of 2 mechanical, 1 electrical, and 3 software engineers to begin the development of such a device in the form of a feasibility study.
Final Automated Drone Base Prototype
We designed and built a portion of a fully functional system, consisting of a drone which is able to fly pre-programmed routes and a base that will house, charge, and release the drone. The design takes a modular approach, separating the components into the the drone and control electronics, the charging system, and the physical base station. This development accelerated Subsurface Insights towards their goal of augmented data collection.
Skills Learned:
Research and design of automated drone base systems.
Knowledge on drones.
Counterweight systems.
Role:
Mechanical Engineer in charge of creating a base system that houses and re-centers the drone to land on charing pads for self charging.
Automated Precision Landing Test
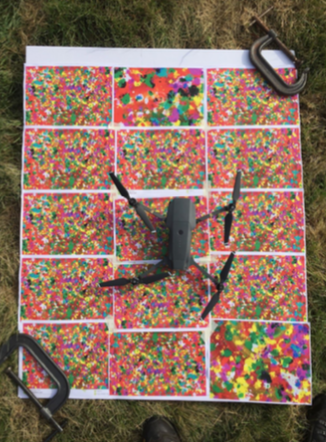
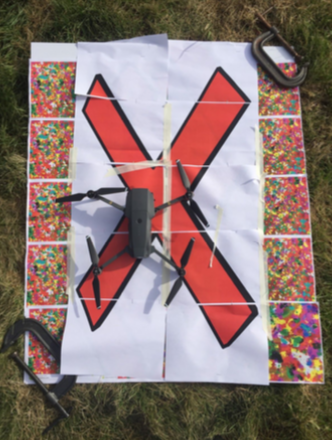
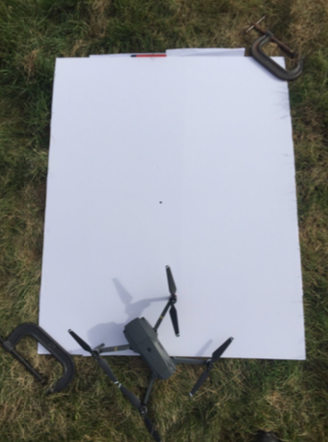
Among the many aspects of the autonomous drone system, landing is the most critical forsuccessful operation. The drone base relies on accurate and successful landing of the aircraft for charging, data transfer, and consecutive flights. Without successful landing, the system would no longer be fully autonomous and would require manual adjustment between flights. Considering these design constraints, a system that combines both mechanical and electrical solutions will be implemented to maximize landing accuracy and device simplicity.
When conducting trade research on precision landing solutions, the onboard DJI precision landing function stood out as the best choice due to its claimed accuracy and the fact that the system has already been implemented in the drone and tested by DJI. The onboard DJI landing system reports a landing accuracy radius of 0.3 meters, using a combination of GPS and vision based landing system.42 Before selecting this solution for a prototype, a series of tests were needed to verify the reported accuracy by DJI. The testing was designed to determine how accurately the drone would return to the exact place of takeoff and whether distinct home patterns affected sensitivity of the vision system. The Mavic had a maximum deviation from takeoff point of 0.5 m, demonstrating the ability to reliably land within within a 1 m radius.
Drone Centering Mechanism
Despite the high accuracy of DJI’s precision landing system, there is still a considerable error. As a result, an additional system is required to center the drone to a repeatable position to facilitate charging and ensure the system has a uniform takeoff condition and home point. It was determined through testing that a mechanical system would produce the most consistent results with the lowest level of complexity and required integration. Several techniques were considered, including a cone centering system, magnetic system and actuator arm system. Ultimately, the actuator arm technique was selected, utilizing a geometry discovered during testing that allows the system to only consist of two actuator arms for centering rather than four.
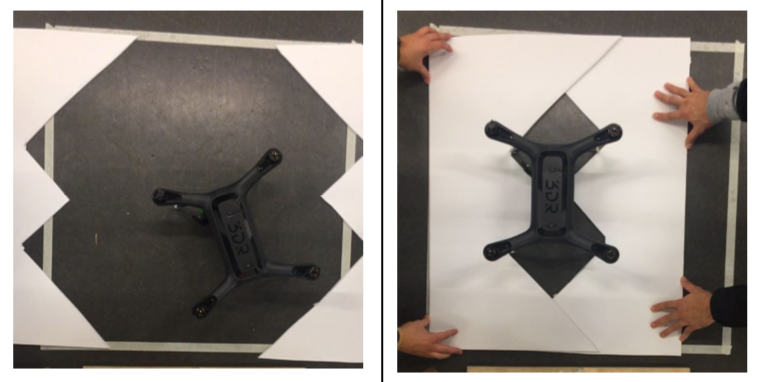

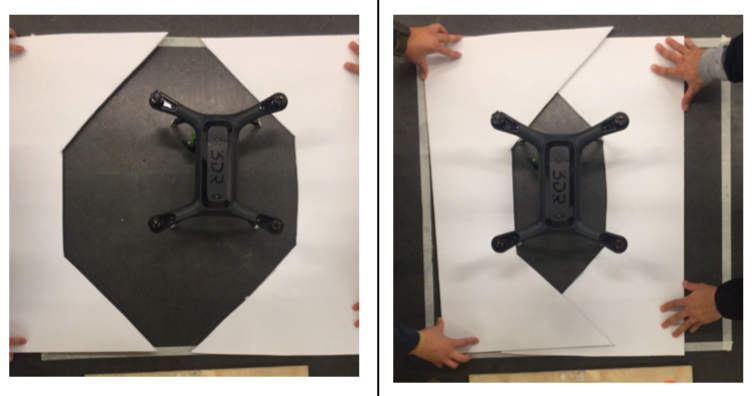
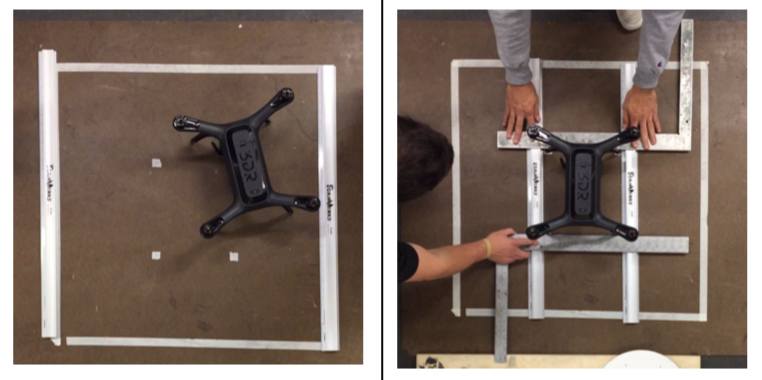
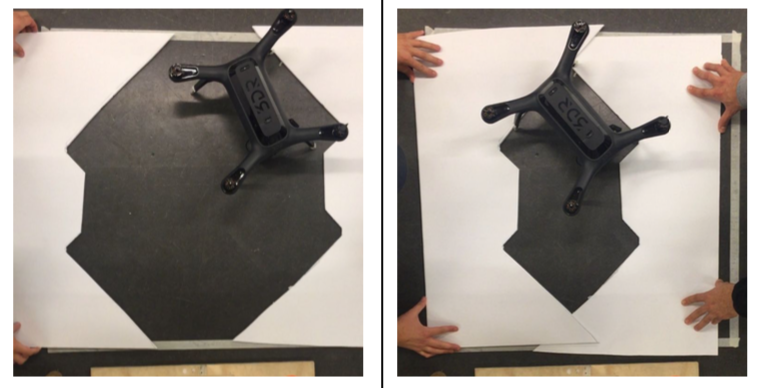
Base Design
Test results indicated that drones can successfully launch within a square area, but have difficulty landing within enclosed walls due to horizontal drifts and turbulence. As such, the launch pad must remain clear of the base walls or components to minimally interfere with drone landing. Furthermore, the base must have a dimension of at least 1 meter by 1 meter to account for deviation from the center. Research on weatherproof boxes was conducted to determine whether to use a pre-existing box and modify it to fit the needs of the drone or create a proprietary box. In evaluating the needs of the complete system, analysis was completed on how the drone accesses the landing pad, how the mechanics of the door contributes to an automated system, and the ease of integrating a mechanical centering device. Most pre-existing box options provided multiple complexities such as design integration of a rising platform, size of box, as well as modularity of door design. Building a proprietary box would allow for exact dimensions specified by the automated precision landing test and easy modifications that would cover all the required specifications and needs of the drone.
Reliable landing requires a landing pad clear of enclosed walls. Therefore a method to reveal the launchpad from within the base is necessary. In evaluating different launchpad uncovering methods, analysis was completed on the complexity of the door mechanics, the integration of a mechanical centering device, as well as the flight interference for both launching and landing. Launch pad uncovering methods was narrowed down to the barrel rotation.
The barrel rotation mechanism uncovers the launch platform by simply rotating a cylinder like structure about and underneath the launchpad. There is no need for an additional raising of the launch platform as the launch pad will be clear of enclosed walls after rotation.
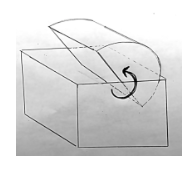
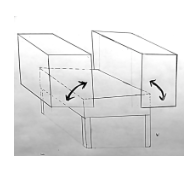

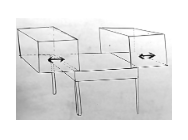
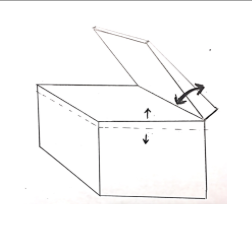

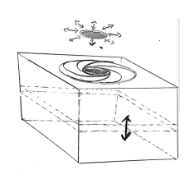
Solidworks:
Details:
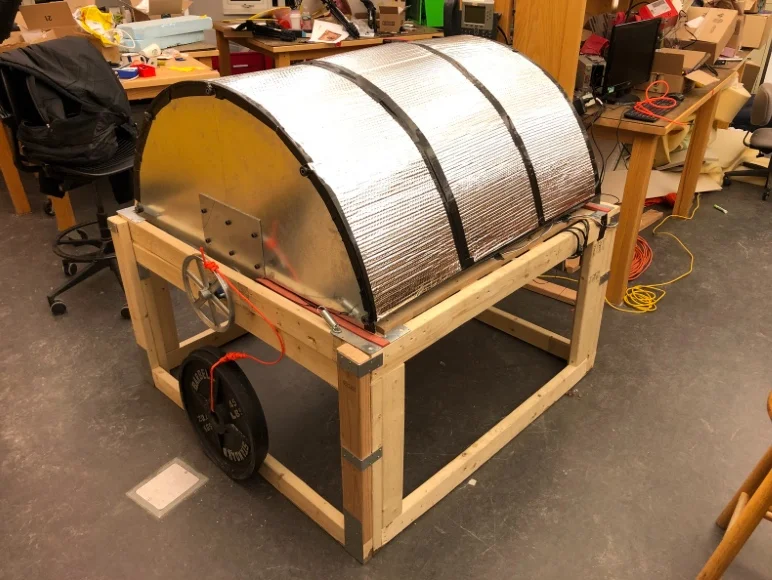
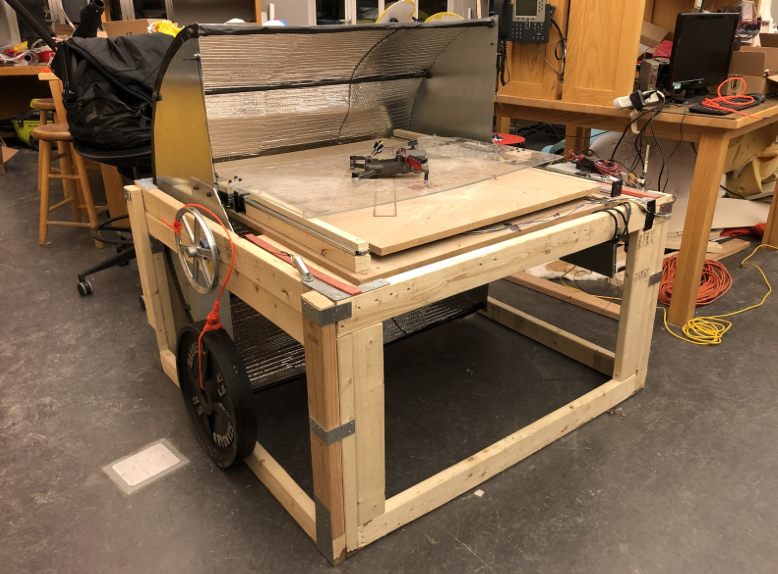
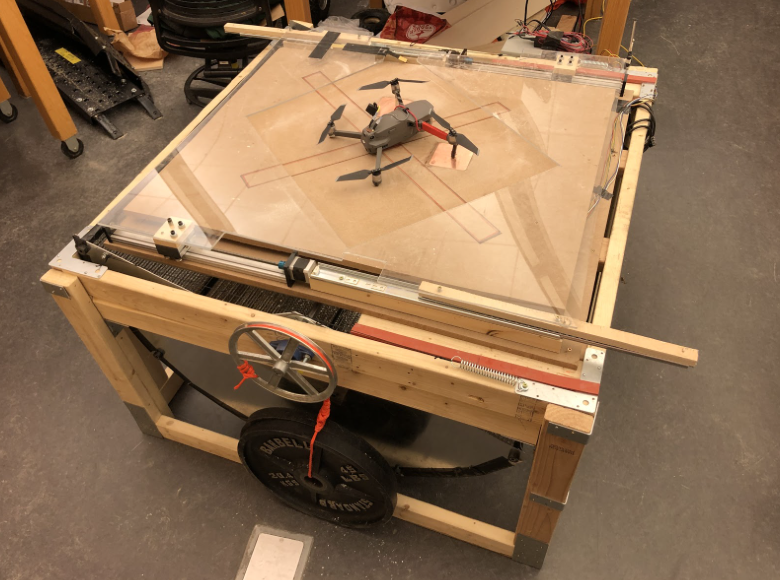

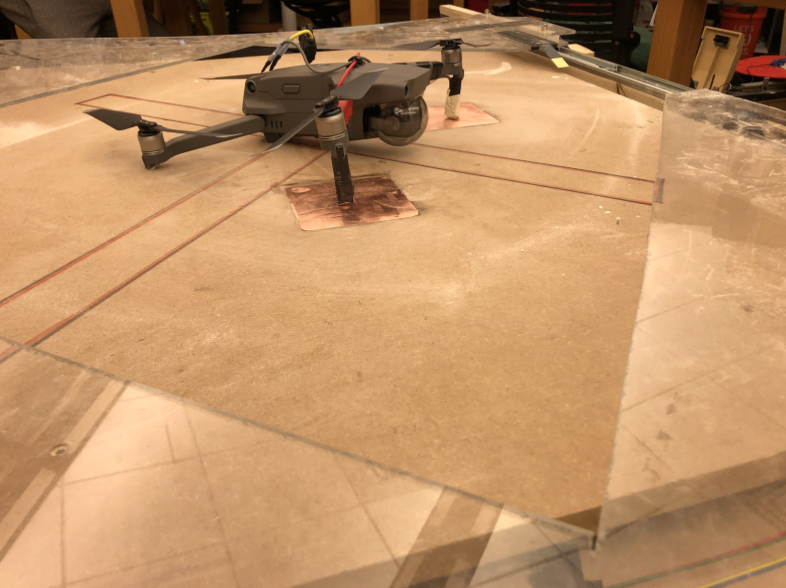
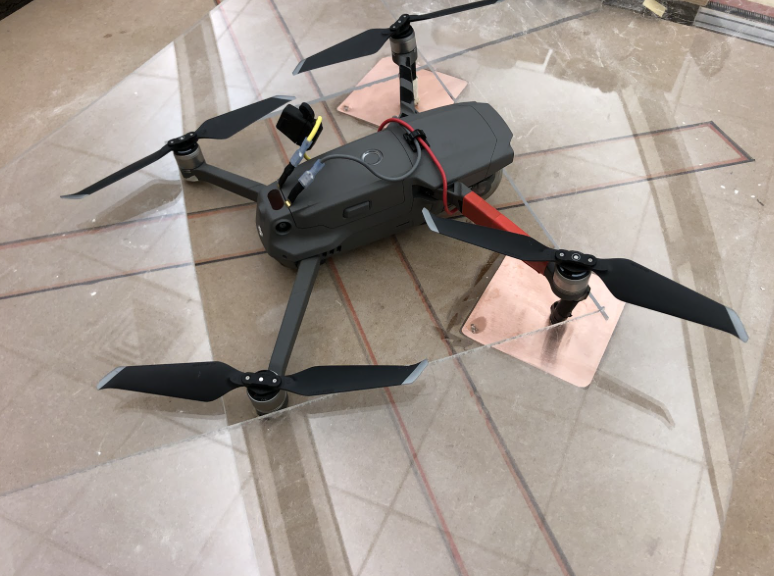
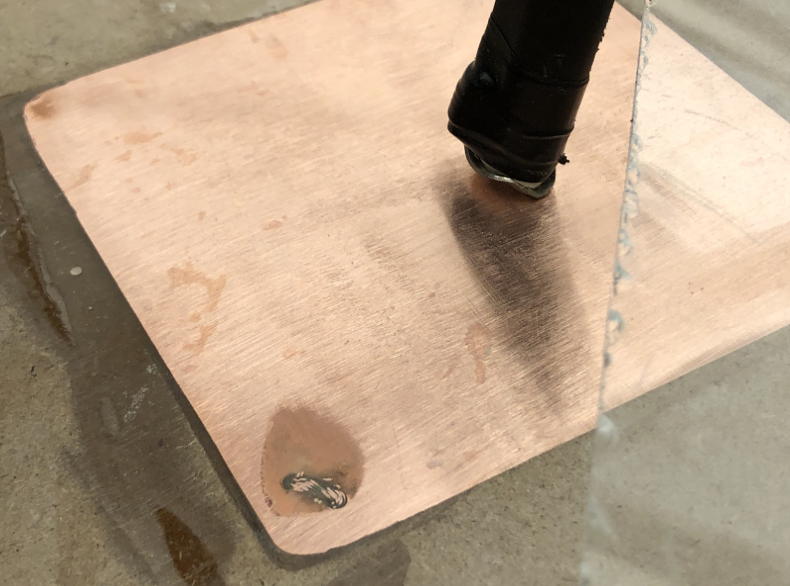
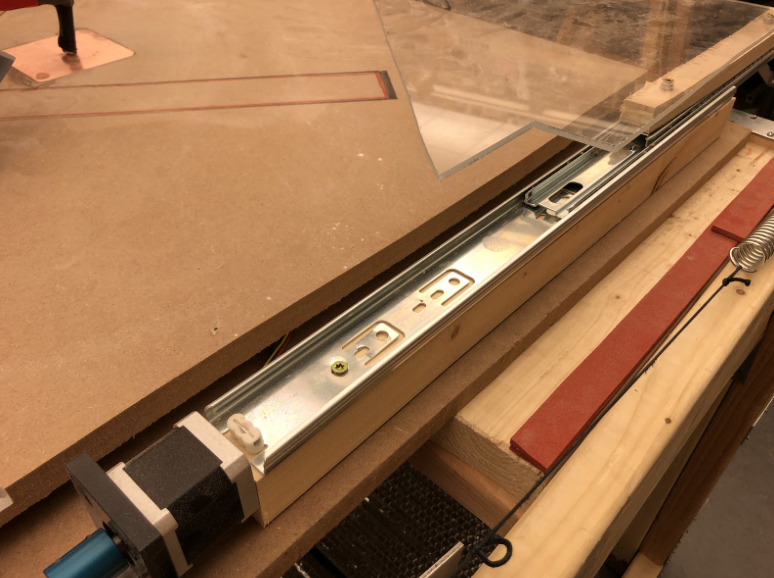
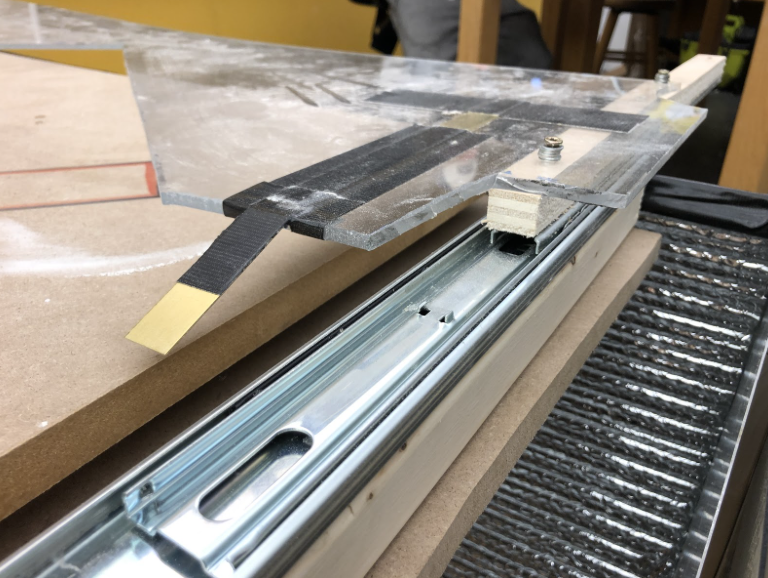
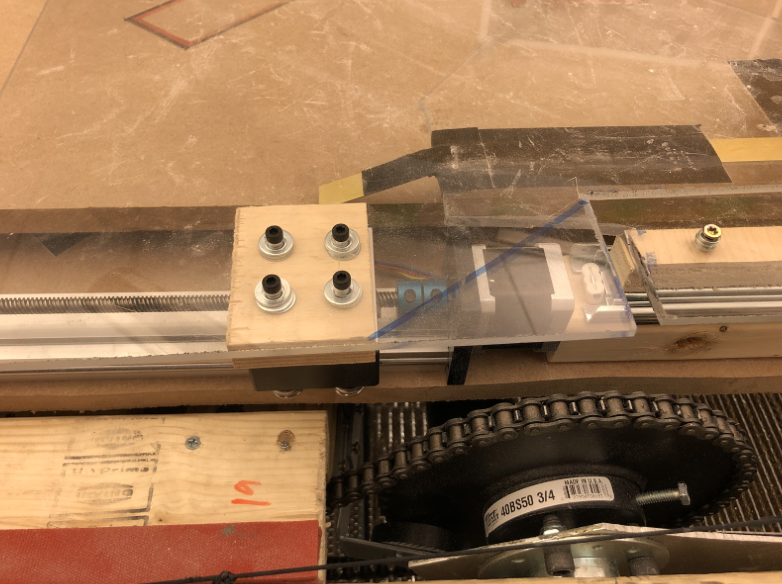

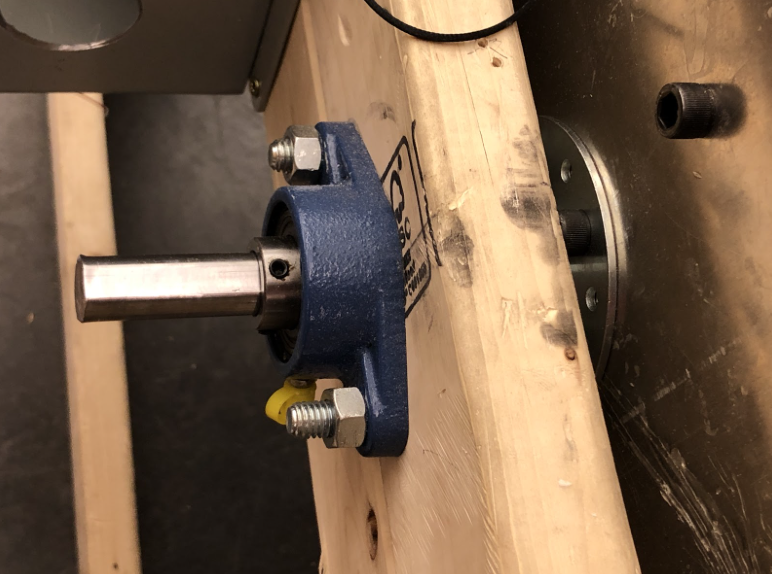
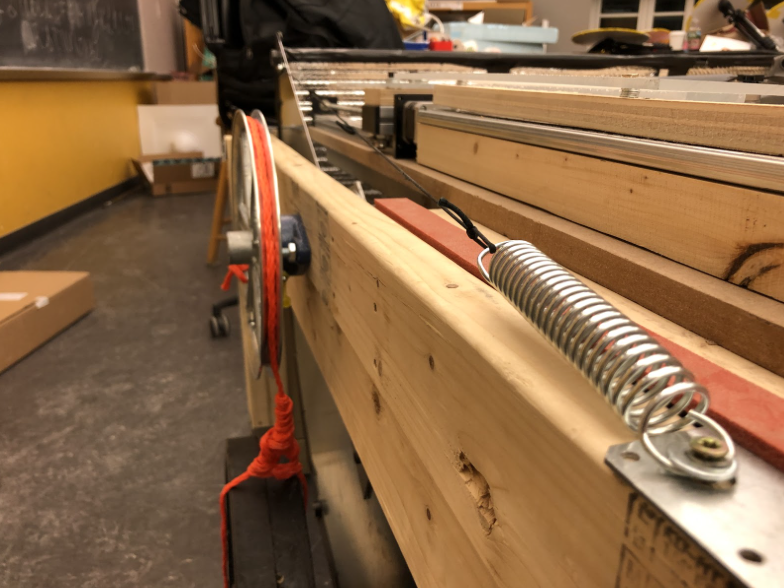
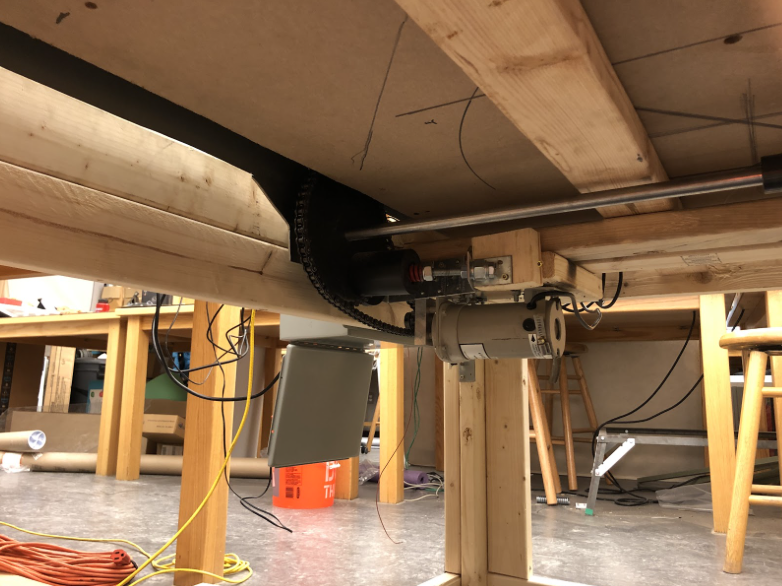

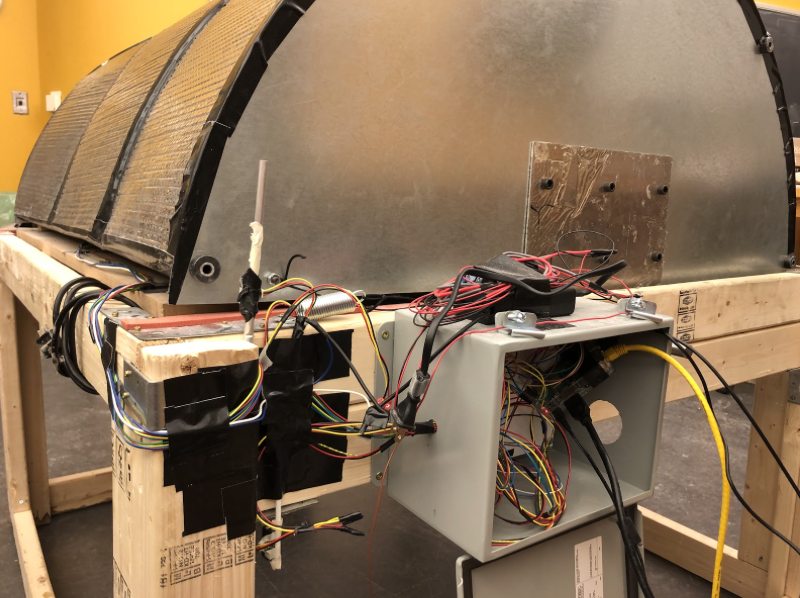
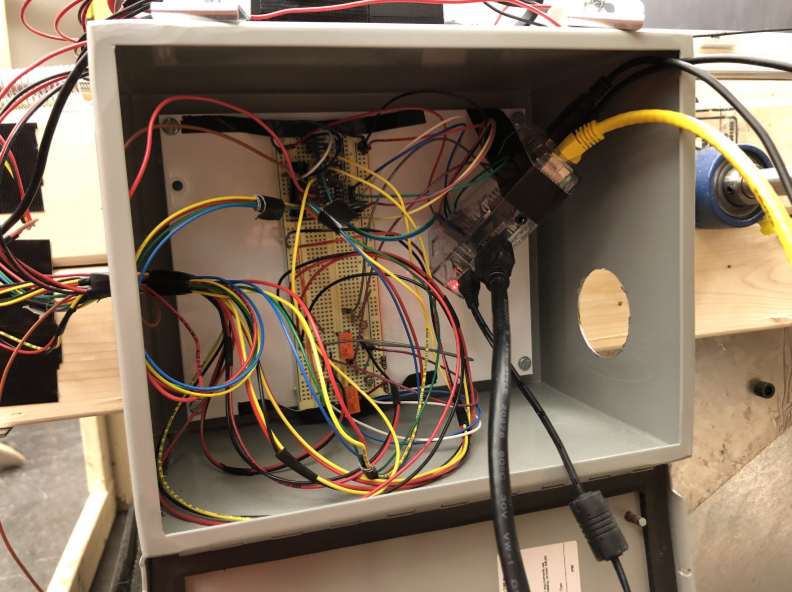
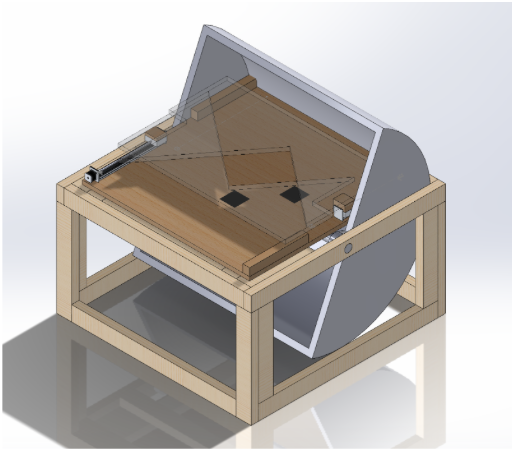

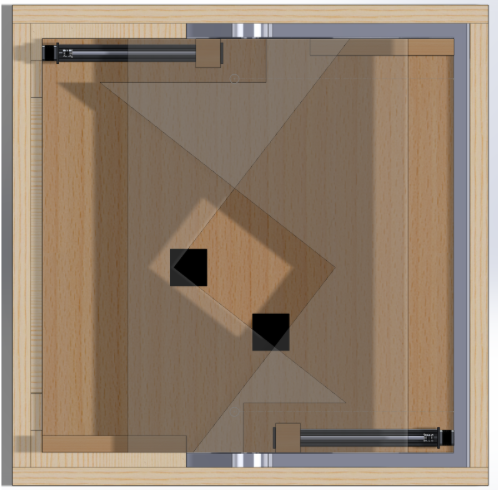
