AquaCool
Problem Statement:
There is currently no rapid and effective emergency method to address unexpected heat stroke in remote outdoor environments.
Solution:
We plan to build a water bottle cap consisting of one CO2 gas cylinder to rapidly cool water, and a mist nozzle to spray the water. Applying cold water mist to a large surface area of skin will cool the victim so that she/he can be transported to the hospital before organ failure occurs.
Skills Learned:
Research current state of the art cooling devices.
Research thermal properties of expanding air cooling devices.
Prototyping through trial and error.
Role:
Research/Design/ Prototype AquaCool
Conclusion:
Our testing has proven that our product is a success. Our prototype testing demonstrates that our product can use compressed gas to cool water by an enormous amount (at 22.0 degrees, it exceeds our 15.0 degree cooling expectation by nearly 50%), our tissue phantom testing proves that our cold water evaporative cooling method is superior to all alternatives (beating the next best one by nearly 40%), and our human testing shows that our product can significantly lower the human body temperature (dropping CBT by 0.57 in just 10 minutes). We have a product design that is lightweight, easy to use, and interfaces with standard Nalgene water bottles. It should be a clear choice for any safety conscious hikers or wilderness EMTs to purchase our product to defend against the rising threat of heatstroke.
First Prototype:
For our first prototype we attached a bicycle-pump-style release valve to a 16 g canister of CO2, and submerged the canister in 0.2 L of water. Releasing the gas from the canister into the air cooled the canister, allowing it to cool the water. We did a test to measure thermal efficiency, releasing the gas and recording the temperature change of the water: a drop of 2°C.
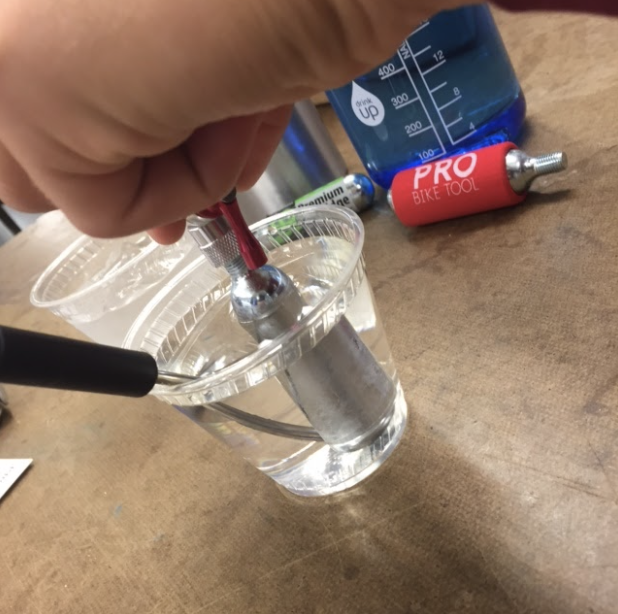
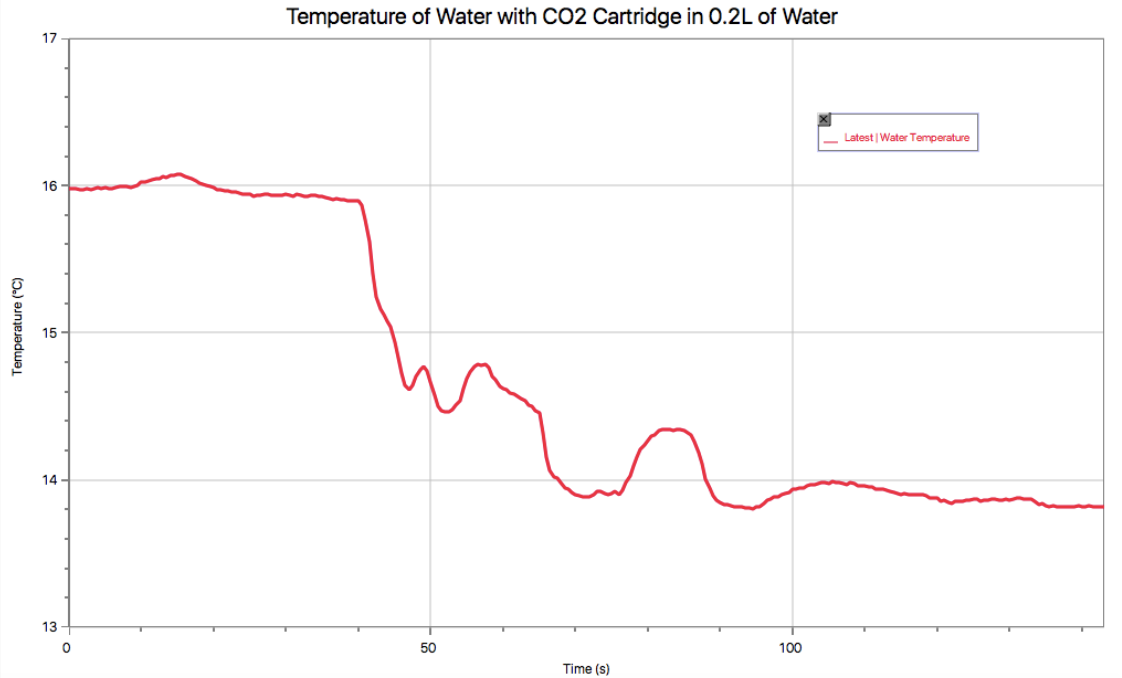

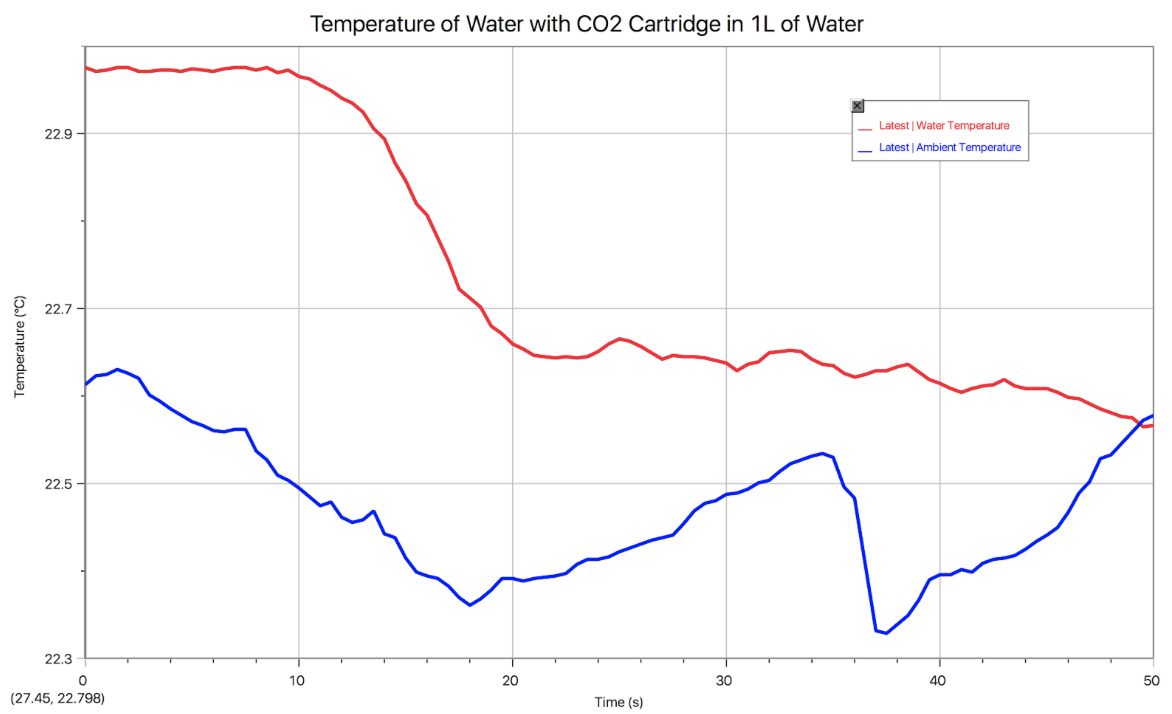
Second Prototype:
We constructed our second prototype by drilling a hole in a Nalgene bottle cap and mounting our canister there, submerged in the 1 L of water in the bottle. We did a new thermal efficiency trial, releasing 16 g of compressed CO2, but this time submerged in 1 L of water. The water’s temperature dropped by 0.4°C.
Third Prototype:
Our third prototype is a 3D printed preliminary “looks-like” prototype designed to help us visualize the final appearance of our product.
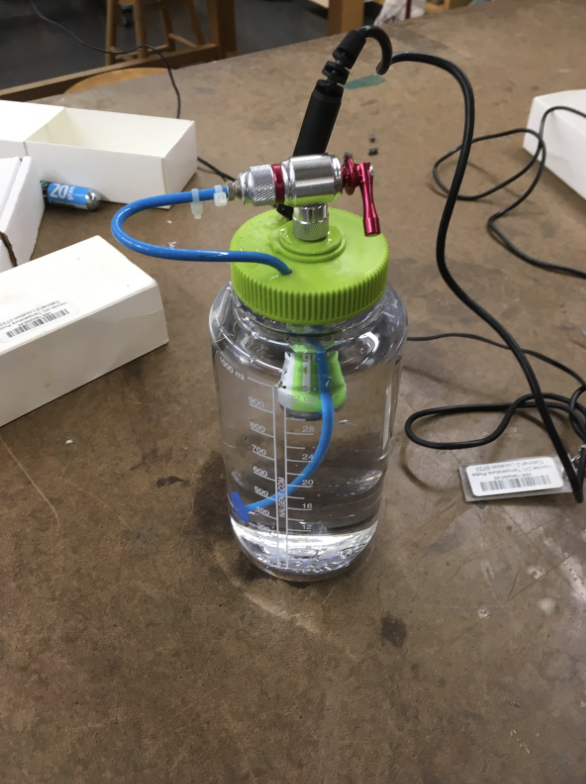
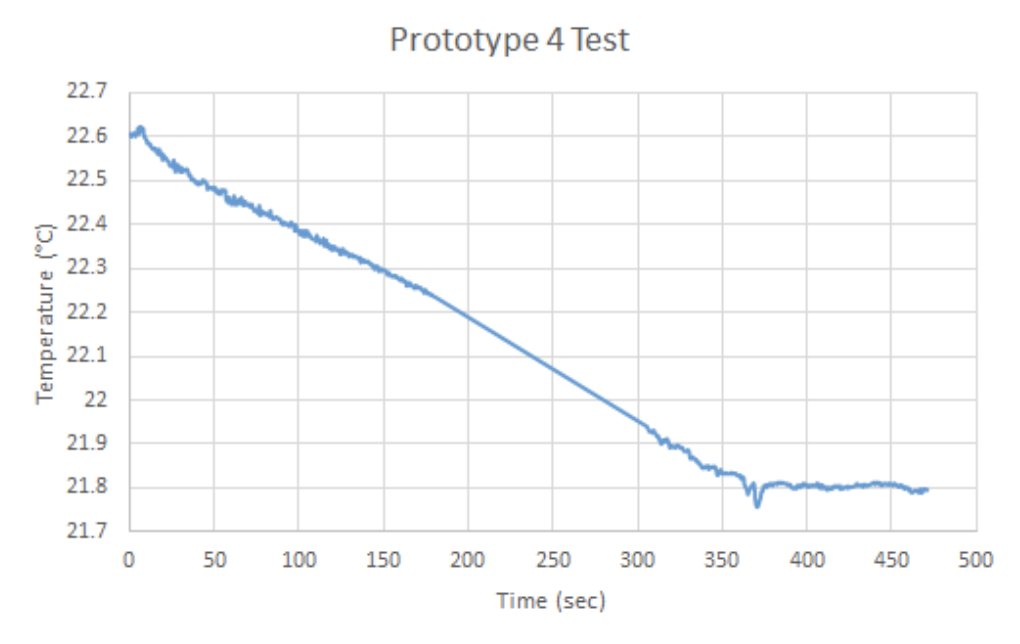
Fourth Prototype:
Our fourth prototype was identical to our second, except for the addition of a hose directing the released gas to the bottom of the bottle. This serves 3 purposes: it stirs the water, making the cooling even, it brings the cold air in contact with the water, increasing our cooling, and it slows the release of the gas, meaning the cooling is no longer an adiabatic process. It cooled 1 L by 1°C with 20 g CO2.
Fifth Prototype:
We made two alterations from the previous version: we increased the size of the canister from 20 g to 100 g, and we changed the gas from CO2to Diflouroethane (DFE). We were able to get large canisters of DFE more easily than CO2. This test cooled 0.6 L by 7.2°C with 100 g DFE.

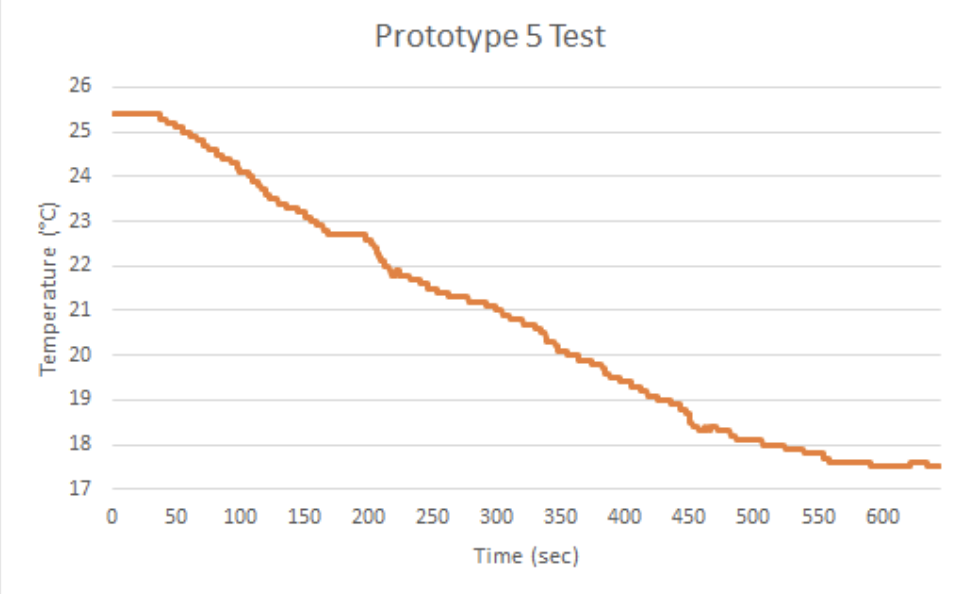
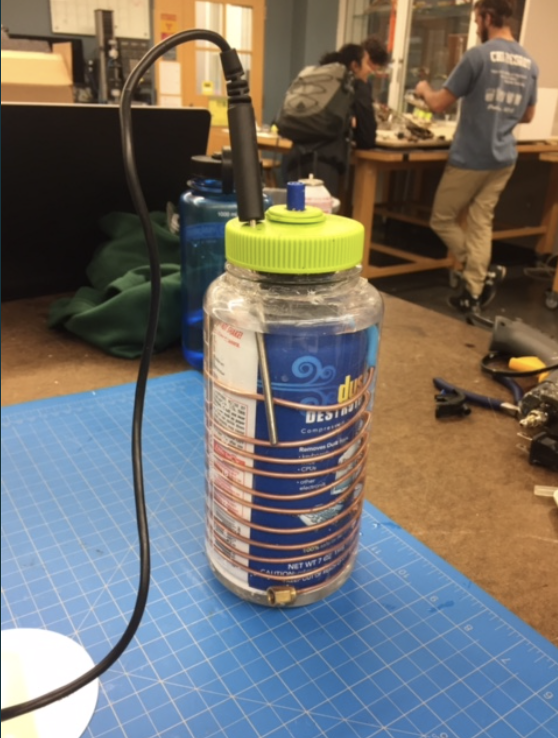
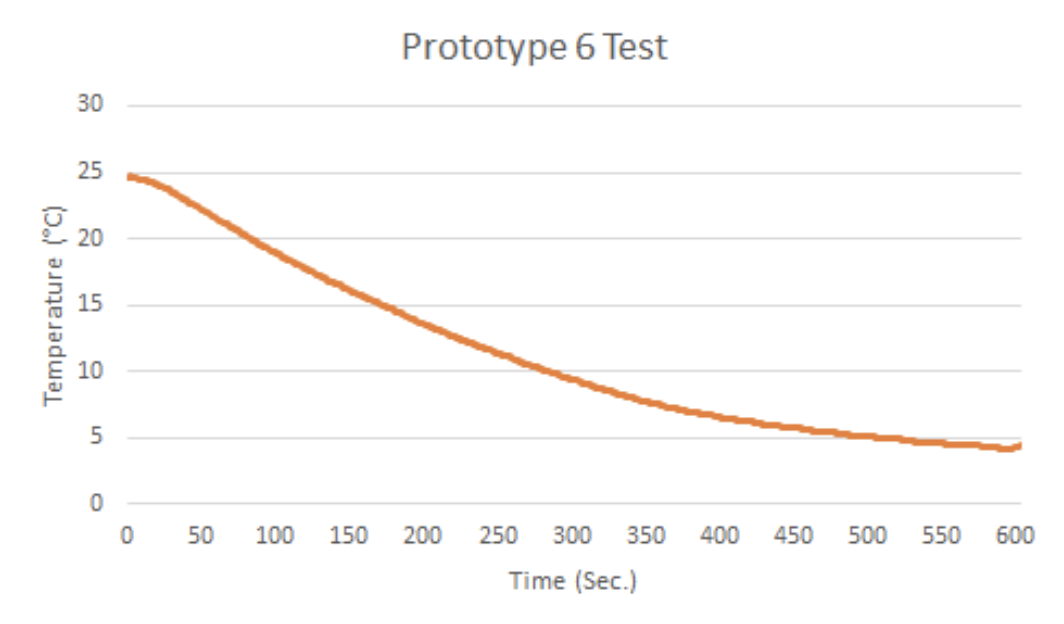
Sixth Prototype:
This prototype increased the size of the canister to 200 g and replaced the tube leading to the bottom with a copper coil. The coil’s increased length and thermal conductivity relative to the tube further increased our cooling efficiency. The sheer size of the DFE canister limited the water in the bottle to 500 mL of its 1 L maximum capacity. This prototype was wildly successful, cooling 0.5 L of water by 20.4°C, an excess of what we require in both water and cooling.
Seventh Prototype:
This prototype used the same core design as our sixth, but with two quality-of-life changes. First, we altered the ventilation system to reduce the amount of water that splashed out of the container during cooling. Then we replaced the manual continuously-held gas release button with a screw that could be tightened once and left until the process ended. In testing, it cooled 0.5 L of water by 22.0°C.
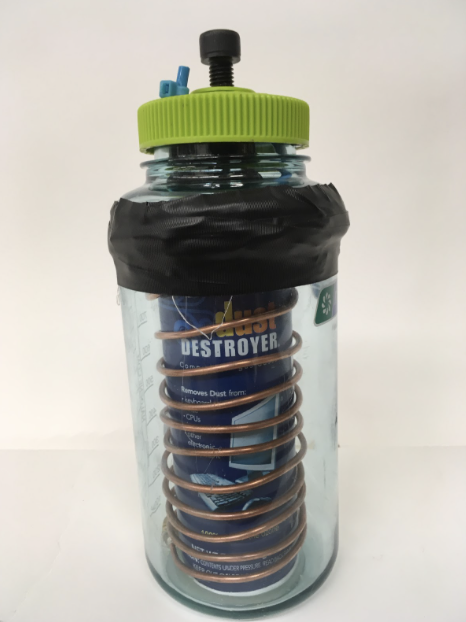
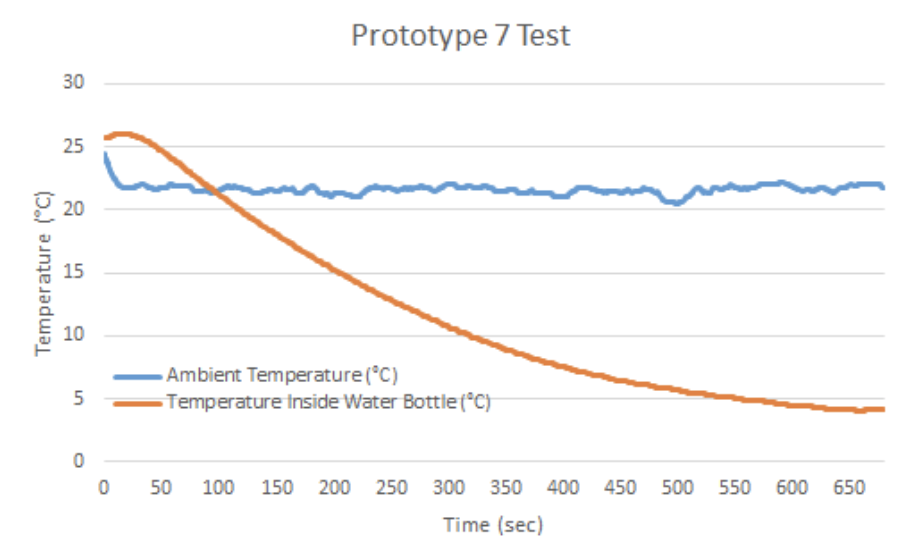
Eighth Prototype:
This prototype was 3D printed as a representation of what our final product should look like in its market-ready state. It also included a copper coil and a dummy gas canister, making up the 3 parts of our product.
AquaCool will consist of three distinct items; the polypropylene cap, the copper coil, and the CO2 canister demonstrated in the figures above. The polypropylene cap in itself will include a misting device, a device that will safely puncture the CO2 canister, and dispersion mechanism that will redirect the CO2 into the copper coil. Not only will the copper coil redirect the CO2 towards the bottom of the bottle, but the cold gas will also cool the copper tubing, which will then cool the water. This copper tubing increases the time duration in which the cooling agent of the gas stays in contact with the water. The redirected gas by the copper tubing will stir up the water, which will allow the water to be uniformly cooled. The gas will then seep back up to the polypropylene cap, and escape through carefully placed holes, in order to prevent any build up pressure within the bottle. Through this process, AquaCool cap will be able to drop 16 ounces ambient water temperature by about 20ºC.
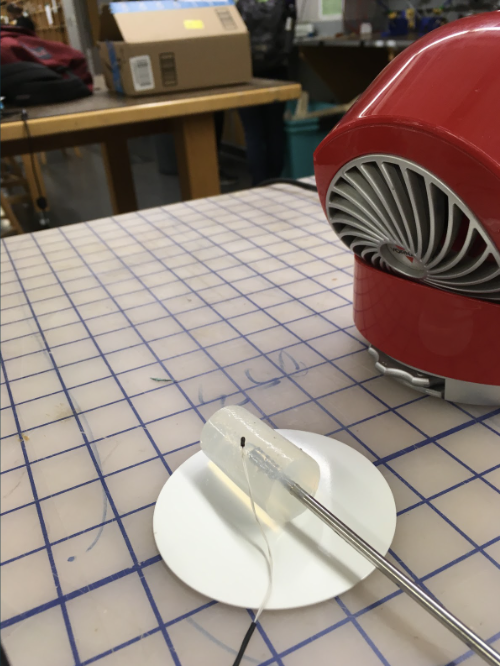

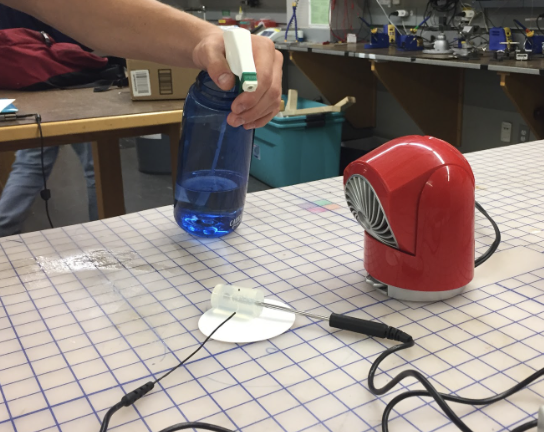


Tissue Substitue Testing:
We needed to prove that cold water based evaporative cooling was superior to state of the art emergency cooling. To do so, we created a small cylinder of 1% agarose 99% water around a Vernier temperature probe. We applied our various cooling methods to the agarose, measuring the internal temperature, external temperature, and ambient temperature over the course of 10 minutes.
The trial corresponding to our product, the Cool Water Misting with Fan, is the most effective cooling method, meaning that our product is superior to the state of the art. It is also worth noting that our product beats the runner up, Warm Water Misting with Fan by 40%, indicating that cooling the water does have a large impact on its cooling potential, even with a fan involved.